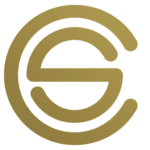
Proportional-Integral-Derivative (PID) control theory is a widely used control method that is based on the feedback principle. This control theory is used in various applications such as temperature control, speed control, and position control of mechanical systems. It operates by continuously adjusting the control signal based on the difference between the desired setpoint and the actual process variable. Here we’re going to discuss the pros and cons of the PID control theory and when it should be used instead of other control methods, as well as to address the issues related to nonlinear systems and constraints.
One of the main advantages of PID control is its ability to provide fast and accurate control of dynamic processes. The proportional term of the control equation compensates for the error between the setpoint and the process variable, and the integral term eliminates the residual error. The derivative term, on the other hand, provides additional control action based on the rate of change of the error, which helps to stabilize the control system. These three terms work together to provide a fast and accurate response to changes in the process variable. Another advantage of PID control is its ease of implementation. PID control can be implemented using simple analog electronics or software algorithms, making it a versatile and accessible control method for a wide range of applications. It also has a simple mathematical structure that makes it easy to understand and modify for specific applications.
However, PID control is not without its disadvantages. One of the main limitations of PID control is its sensitivity to process disturbances and measurement noise. This sensitivity can cause the control system to oscillate and overshoot the setpoint, leading to poor control performance. Additionally, the controller may become unstable if the gain parameters are not set correctly, which can cause the control system to become unstable and unpredictable.
PID control is typically used for linear systems, but it can also be applied to nonlinear systems with appropriate modifications. Nonlinear systems are more complex than linear systems and can exhibit behavior that is difficult to predict. In order to control nonlinear systems, it is often necessary to linearize the system around a operating point and then apply PID control. However, this linearization process can lead to a loss of accuracy, and alternative control methods, such as nonlinear control methods, may be more suitable for these systems.
Another issue that can arise when using PID control is the presence of constraints on the control signal. In some applications, there may be limits on the control signal, such as a maximum or minimum value, or a rate limit. These constraints can affect the performance of the control system and may cause the control signal to become saturated. This can result in poor control performance and even instability. To address this issue, it may be necessary to incorporate constraint handling techniques into the control design, such as anti-windup or gain scheduling.
In conclusion, PID control is a widely used and versatile control method that offers fast and accurate control of dynamic processes. However, it has limitations, and alternative control methods may be more suitable for specific applications, especially for nonlinear systems or systems with constraints. When choosing a control method, it is important to consider the specific requirements of the process and the available resources for implementation, and to choose a control method that is appropriate for the specific application. Alternative control methods, such as nonlinear control or constraint handling techniques, may be more suitable for these systems, and careful consideration of the trade-offs between these methods is crucial for achieving optimal control performance.